DCS系统(Distributed Control System,分布式控制系统)和PLC(Programmable Logic Controller,可编程逻辑控制器)在工业自动化领域中扮演着重要角色,但它们在多个方面存在显著的区别。
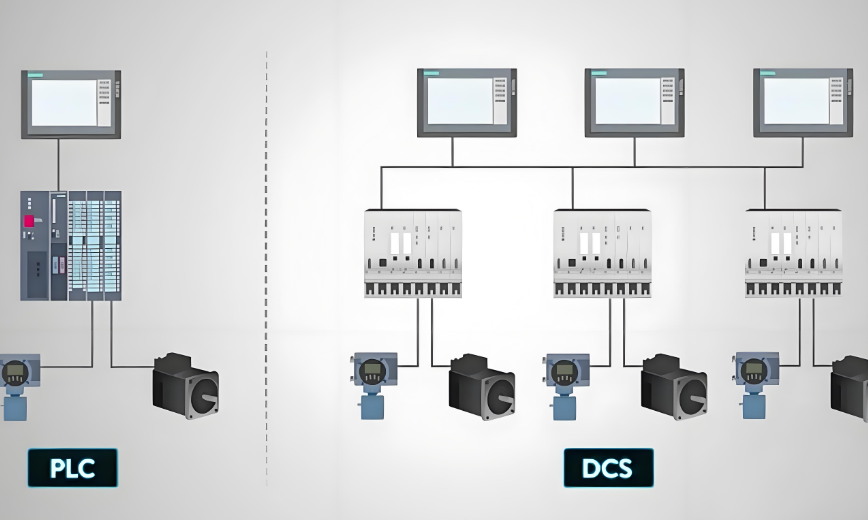
一、定义与基本概念
1、DCS系统:DCS是一种高度集成的、模块化的、分布式的控制系统。它采用集中监控和分散控制的方式,实现对工业过程的自动化控制和管理。DCS系统通常由多个控制节点、通信网络、操作站、工程师站等组成,具有高度的可靠性、灵活性和可扩展性。
2、PLC:PLC是一种用于工业自动化控制的电子设备,它采用可编程的方式实现对机械设备、生产过程等的控制。PLC具有高度的可靠性、灵活性和易用性,广泛应用于各种工业领域。
二、组成与结构
1、DCS系统:
(1)控制节点:负责实现对工业过程的实时控制,采用高性能的处理器和专用的控制算法。
(2)通信网络:实现各个控制节点之间的数据交换和通信,通常采用高速、可靠的通信协议。
(3)操作站:用户界面,用于实现对工业过程的监控和管理,采用图形化的人机界面。
(4)工程师站:配置和维护界面,用于实现对控制策略、控制参数等的配置和维护。
2、PLC:
(1)中央处理单元(CPU):核心部件,负责处理输入信号和控制输出信号。
(2)输入/输出模块:与外部设备连接的接口,用于信号的采集和控制。
(3)电源模块:为PLC系统提供稳定的电源。
(4)编程器/编程软件:配置和维护工具,用于实现控制策略和控制参数的配置。
三、功能与特点
1、DCS系统:
(1)实时控制:采用高性能的处理器和专用的控制算法,能够实现对工业过程的实时控制。
(2)数据采集:实时采集工业过程的各种数据,并进行处理和分析。
(3)监控和管理:具有图形化的人机界面,方便用户进行监控和管理。
(4)通信和数据交换:采用高速、可靠的通信协议,实现各个控制节点之间的数据交换和通信。
(5)可扩展性:采用模块化的设计,具有高度的可扩展性。
2、PLC:
(1)逻辑控制:实现对机械设备、生产过程等的逻辑控制。
(2)顺序控制:能够实现对生产过程的顺序控制。
(3)定时和计数:具有定时和计数功能,用于控制生产过程中的时间和数量。
(4)数据处理:对采集到的数据进行处理和分析。
(5)通信和网络:具有通信和网络功能,可以与其他设备和系统连接和数据交换。
四、应用领域
1、DCS系统:广泛应用于石油、化工、电力、冶金、制药等大型工业领域,特别是在需要高度集成、高度自动化的复杂工业过程中。
2、PLC:广泛应用于机械制造、汽车、电子、食品、包装等工业领域,特别是在需要灵活控制、快速响应的简单或中等复杂度的工业过程中。
DCS系统和PLC在定义、组成、功能与特点以及应用领域等方面存在显著的差异。DCS系统更侧重于大型、复杂工业过程的集中监控和分散控制,而PLC则更适用于离散事件和连续控制的逻辑控制。在实际应用中,应根据具体需求和工程要求选择合适的控制系统。